东方希望,一个重化企业“文淑旭鑫”的数字化转型样本
日期:2023-07-12 14:13:48 / 人气:287
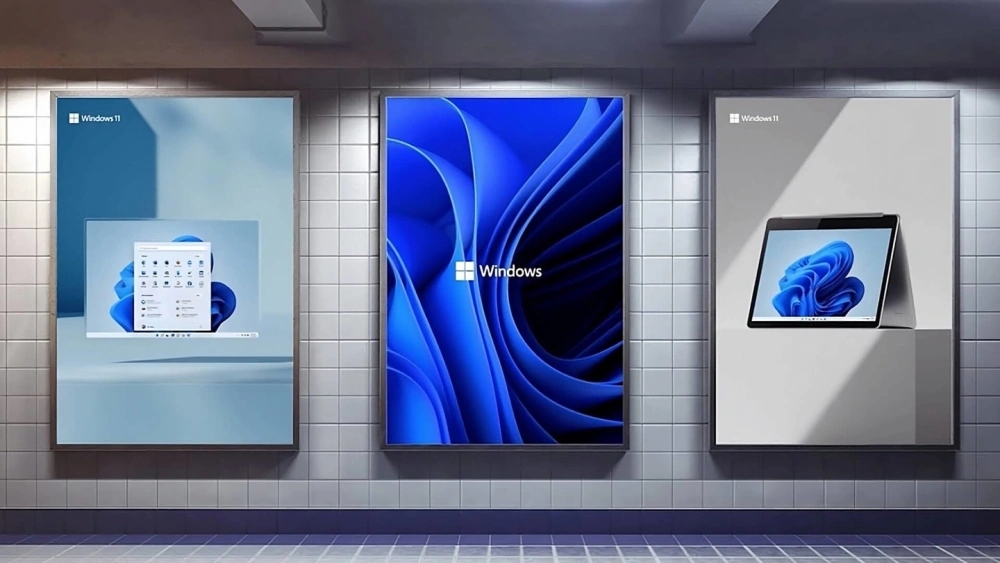
在电解铝厂工作多年的李江涛发现,他的工作正变得与一组颜色密切相关。红色、橙色、黄色和绿色。
黄色为一级提醒,橙色为二级预警,红色为最高级别报警,绿色代表正常运行。
作为东希望新疆准东园区的维修技术工程师,他的工作是保证电解铝生产车间电解槽的正常运行。
自从应用数字化技术打通工厂的MES和钉钉后,这个重化车间的所有设备故障都能自动上报到相关人员的手机上。
李江涛和他的同事们只需要调整相关的工艺参数,消除各种颜色的预警信息,工厂的安全生产隐患就可以大大减少,生产的非正常中断也可以大大减少。
在重化工业中,安全生产和业务规范被视为与运营效率同等重要。
围绕这些安全生产目标,行业沉淀了无数的操作规范、行为方式和工作流程。随着数字化革命的深入,一批先锋企业正在加速将这些过去的运营实践与新兴技术相融合。
在位于新疆昌吉五彩湾的东希望准东循环经济产业园,东希望集团数字化子公司东西科技正在探索数字化技术实现业务规范、降本增效、安全生产的应用路径,针对园区铝工业、硅工业两条产业链,
以电解铝生产异常自动报警为例,这个高效、协同、互联的数字化平台正在帮助企业打通IT和OT设备,实现高风险作业的实时控制和闭环管理。
数字技术在重化工业核心生产环节的应用,正在推动“人人关注安全,人人都会应急”的实现。
在电解器前“消除红色”的人
一年四季,李江涛车间的工人每天都要戴上红色头盔、银色隔热服、防护口罩和防烫手套。在温度较高的电解槽下,用测温枪测量电解槽的三个温度,手动监测并记录上报点的温度。
对异常数据进行人工判断,然后对异常温度进行拍照并反馈给工区管理组,工区安排人员对异常进行处理,确保电解槽安全稳定运行。
这一工作要求与电解铝生产工艺的特点密切相关。
在庞大的电解铝生产车间里,每个电解槽都是一个反应炉,内部会发生剧烈的电化学反应,从而产生液态原铝。
还原后的铝液鲜红,温度高达900度。
冷却后可加工成铝锭、铝合金圆锭,最后可制成苹果手机、笔记本电脑外壳、高铁轨道等各种日用铝制品。
巨大炉内的电化学反应24小时不间断,但反应过程并不以同样的强度和均匀性发生,反应过程并不安全。
比如电解槽长时间在高温环境下运行,可能会变形,铝液会通过缝隙渗入电解槽的保护层。
“像旧食槽一样,它的炉膛越来越薄。如果不及时补充,就会在最薄弱的地方发红发亮。最后,整个槽中的铝水和电解质将会流出,整个地面将会爆炸,”李江涛说。
类似的影响生产安全的因素可能有50多个。比如阴极碳块和阳极碳块形成的闭环电流并不总是均匀地通过碳块;
电解液的配比、碳块的新旧程度、导电率都会影响反应进程,最终可能出现行业内的“漏槽”、“轧铝”等生产异常中断,带来几百万甚至上亿的损失。
当然,肉眼很难了解这些复杂设备的操作细节。行业内的常规做法是通过温度来判断罐内的反应。
工厂管理者也意识到了这种人工测量机制中存在的问题,比如随意性,缺乏实时性,信息报告和反馈可能不及时。
一些团队成员有很强的责任感。如果他发现问题并积极报告,他可以防止生产中断。
但如果团队中的管理者下班后看不到报表信息,不能及时调整工艺参数,就可能造成巨大的损失。
将数字化技术应用于化工生产的安全生产,构建一个实时、自动的报警系统,已经成为工厂管理者和数字化服务提供商思考的解决方案。
首先,通过自动测温设备解决了温度实时准确的问题。
电解槽侧壁和底部安装了数十个自动测温装置,在MES设备上可以实时看到温度信息。每个点根据黄色、橙色、红色的严重程度设置提醒机制。
其次,MES设备上的信息与钉钉的组织和业务流程对接,让过去只有少数人在专门设备上才能看到的信息,在组织中自动定位到相关层级。
“黄色推给班长技术员,橙色推给工区主任、班组长,红色推给厂长。”
李江涛介绍,推送异常信息时,会附上一张表格,需要填写处置方式和结果。
如果消息处理者没有权限处理相关的流程,可以选择上级的帮助,最终实现报警信息的闭环处理。
有了这个系统,再也不用时刻带着测温枪穿梭在电解槽之间了。而是通过扫描设备上的二维码,打开钉钉,就可以监测到电压、温度、针振等各种设备数据指标。
他们的工作重心也发生了变化,通过流程操作消除了橙色、黄色和红色设备的报警信息。
比如电解液配比不均匀就加电解液,如果槽内出现杂质就安排专人刮除,保证槽内电化学反应正常安全。
同时,与安全生产相关的指标也大大提高。
数据显示,漏铝、轧铝事故概率降低90%,异常处理时间缩短50%,异常人员响应效率提高87%。
一位现场操作人员介绍,数字化手段还实现了对设备更精细化的管理,进一步降低了生产成本。
“原来的设备需要在4.07V左右的电压下运行,现在可以更精细地管理设备,只需要4.02V左右就可以运行。一吨铝省150度电,我们厂一年产能80万吨。”
从移动办公到业务全面数字化
电解铝生产车间设备自动报警系统是东希望集团整体数字化建设进程的一个缩影。在这个大型企业集团中,数字技术已经进入重化工业的核心生产环节。
东希望集团对数字化转型的探索持续了8年,新兴技术才从边缘场景走向核心环节。
2015-2016年,国内移动互联网格局初步确定。当时,互联网头部企业已经基本完成移动化转型,平台企业的超级app进入亿级DAU时代。
作为横跨重化工业、农业、房地产等行业的业务板块,多元化经营的企业集团东方希望也期望利用平台公司新兴的移动技术,实现集团办公平台的移动化升级。
从2015年开始,这家企业集团的数字部门就一直在市场上寻找移动办公解决方案。
作为企业协作领域的重要玩家,钉钉就在这个时候进入了他们的视线。沟通完需求和经验后,东希望集团数码部开始尝试钉钉。
现在是东希望集团CIO的王东,当时是数码部门的骨干。
他回忆说,在试用过程中发现,钉钉作为即时通讯软件的一些功能,比如“钉钉”功能、已读未读功能,可以大大提高组织内部的沟通效率。
于是,2015年底,东希望集团总部开始推广使用。到2016年,整个集团用了两个月的时间全力推广钉钉。
当然,东方希望也在不断优化和升级新技术的应用。
在信息化建设初期,该企业集团根据自身业务需求,从外部购买了一部分商业软件系统,包括OA、ERP等与日常办公相关的软件。随着集团数字化转型的持续推进,先后建设了考勤系统、大宗物资、矿山管理、抄表系统、近红外检测系统等。
大宗物料系统最初是按照工厂模式引入的,很难形成统一的业务管理平台。
一旦有新的业务板块和新的业务主体,就需要采购新的系统,很难与之前的系统衔接,运维也非常困难。
此外,过去购买的这些软件缺乏科学规划,设计的操作习惯不符合科学管理的原则,移动性能不足。
这个问题让东希望的数字部门明确,集团未来的数字架构要参考淘宝、支付宝等超级app,构建平台化的能力。
一个系统可以打通之前碎片化的软件和系统。
“不管多少行业,什么场景都应该集中在这个系统上。”
黄是当时东方希望集团的采购总经理,也是数码部门的负责人。他认为只有这样才能满足企业未来发展的需要。
最后,在集团统一移动办公平台的选择上,东希望敲定了与钉钉的合作。钉钉开发了大量开放接口,方便东希望自主开发的业务应用的接入。
2017年是东希望集团业务数字化开始试点的一年。数字化部门的第一个计划应用是智能材料系统。
之前在不同园区,子公司分别从外面购买大宗材料系统,价格昂贵,最终效果也不理想。
经过计算,当时各厂采购的大宗材料系统基本都在20万左右。
但这只是初始版本价格,稍微优化功能还需要12万元。在来回优化下,单个工厂的采购成本在百万以上,整个集团的总成本可能在6000万左右。
“花了这么多钱,唯一好用的就是自动称重功能,进出料的取样、制样、结算等功能都无法实现。”
由于大宗物资系统与其他业务系统没有互联互通,进出新疆准东工业园区的大货车经常要排队3-7天。
基于钉钉开发的智能材料系统上线后,这些问题迎刃而解。一方面,作为软硬件一体化的产品,在新园区部署特别方便。
“整个系统部署在云端,新校区只需要调用接口,插上就可以了。”王东说。
另外它的整体成本要便宜很多,整个集团推广使用的一套系统总成本不到500万。
智能材料系统上线后,实现了园区基本无人值守计量。
以新疆准东的公园为例。之前由3门12人管理。现在只需要4个人轮班管理25台地磅,大大降低了人力成本,同时大大提高了物流运输的效率和取样检测的准确性。
该系统上线带来的效果得到了全集团的认可,加速了东希望业务的整体数字化进程,数字化部门也升级为专业化的子公司东玺科技。
截至2017年底,钉钉已经搭建了70多个业务应用。
技术创新没有止境。
目前,东希望集团的移动应用已经全面钉钉。八年来,东西科技搭建了ERP、HR、MES、安全管理、设备管理、采购平台、销售平台、合同管理等系统,整合钉钉系统总数达到200多个。
钉钉已经成为集团的数字化超级入口,不仅可以在线查看各类业务指标数据,还可以实现各类业务单据的在线备案、流转、审批等一系列闭环管理。
在主营业务板块的生产过程中,除了电解铝生产自动报警系统,钉钉正在全面结合东希望集团的工业互联网平台,实现实时数据采集和“钉钉设备”。
通过钉钉端可以实时显示DCS场景图片,比如多晶硅厂、电厂的DCS图片。生产管理人员已经可以通过钉钉随时随地查看实时工况,指导现场工艺调整,处理异常。
以硅片制造为例,基于工艺流程的生产质量管理系统有效地控制了单晶、加工、切片的生产信息、产品质量状态和设备状态。
通过钉钉平台与各系统的接口集成,可以实现设备异常和炉膛上料的实时通知,有效提高了生产效率。
无人机巡检是最新钉钉的新应用场景。东希望准东工业园占地约20平方公里。传统的检查方式需要保安开车,围栏长达15公里,每两个小时翻一次。至少需要两名保安人员巡逻围栏。
现在,在围栏内有管道的关键位置设置监控点,让无人机进行逐点、周期性的拍摄。
无人机还可以精确重拍,每次都拍摄同一点,这样可以精确对比是否有故障。
现在无人机一小时飞一次,在保安值班室就可以在线看直播和回放。由于无人机还配备了红外系统,因此也可以在夜间使用。
通过这套生产管控系统,目前已经连接了10万台生产设备,实现了7000个关键指标的实时监控,帮助企业解决了数据不透明的问题,形成了对高危作业的实时管理,促进了安全生产。
这个过程并不总是一帆风顺。黄见证了这一过程中组织惯性和技术变迁的磨合。
他分享了一个例子——在数字化建设中,为了提高管理的质量,需要采集更多的数据,实现更细致的管理。但在业务部门得到的反馈可能并不乐观。
“原来业务表单只有五六个字段,但是有了数字控件,需要收集和汇总的数据更多了,表单有五六十个字段。他们极其不舒服。”黄对说:
黄的感悟引起了很多人的共鸣。
在与东希望集团及其下属科技公司东熙科技共同举办的“C10圆桌学堂——走进东希望”专场活动上,现场多位CIO也一致认为,在数字化的某些阶段,管理效率提升了,但业务效率可能会下降。
黄给出的解决方案是在这个过程中同步推进自动化逻辑。在规范流程、格式化数据的同时,根据业务逻辑,可以自动完成一些环节。
东希望集团的整个数字化建设过程也是基于这个理念。他们把自己七年多的技术创新经历分为信息化、数字化、自动化、智能化四个阶段。
信息化阶段,建设重点是基础桌面、网络服务、ERP、OA、邮箱。在数字化阶段,许多工作应该是结构化的、可测量的、可计算的、可分析的、可判断的、可预警的和可控制的。数字化阶段之后是自动化阶段。根据业务逻辑,业务可以在系统中自动进行。
如自动成本计算、自动月结、自动结算、自动评估等。,可以大大减少业务的工作量。
在最终的智能化阶段,企业要充分发挥应用系统采集的数字价值,充分利用人工智能大模型和小模型的能力,实现各项业务和生产管理的自我优化。
在“C10圆桌派——走进东希望”专场活动上,王栋向与会者透露,东希望正在基于钉钉内测的“/”功能,接入依桐千题模型,探索其应用。
在大模型的加持下,一线维修工只要说出自己的故障,就能在钉钉上自动创建工单。
结合企业中沉淀的知识库,大模型可以直接生成解决方案。
这相当于每个维修工都有一个超级助手,大大提高了他们解决问题的能力。“数字化旨在帮助企业取得成功,需要不断创新和升级。”王东说。
在重化工业和大型制造企业中,企业转型和新技术应用的道路并不平坦。
钉钉这样一个高效的合作平台,正在让这些庞大的“巨人”变得更加轻盈,随着数字智能的时代轻松起舞。"
作者:恒达娱乐
新闻资讯 News
- 余男:和王全安同居十年黯然分手...12-17
- 四大天王57岁的黎明,唱功逆生长...12-17
- 网红张全蛋回应热搜争议:没有吃...12-17
- 我是刑警:我宁愿多看拒绝秦川饭...12-17